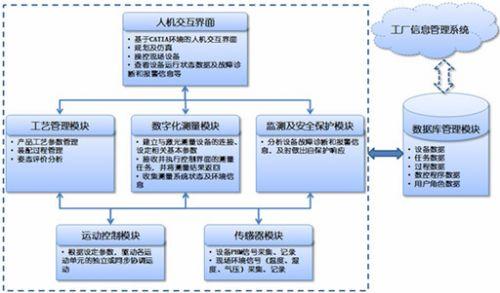
數字化裝配技術體系
中航工業成飛 陳雪梅 劉順濤
飛機裝配技術經歷了從人工裝配、半機械/半自動化裝配到機械/自動化裝配的發展歷程,而目前得到各經濟、軍事發達國家高度重視的數字化裝配技術,正成為現代飛機制造的科技制高點。為了保證飛機日益苛刻的裝配質量要求,滿足機體長壽命要求,提高生產效率,數字化裝配成為必然的選擇。
數字化裝配技術的應用進展
數字化裝配技術不僅包括了傳統數字化裝配概念中工裝的設計、制造及裝配的虛擬仿真等,還包括了諸如柔性裝配、無型架裝配等自動化方法,是數字化工藝技術、數字化柔性裝配工裝技術、光學檢測與反饋技術、數字化鉆鉚技術及數字化的集成控制技術等多種先進技術的綜合應用。
需要強調的是,數字化裝配技術不僅僅局限于軟、硬件設備的簡單堆砌,更在于融合整個設計、制造的數字化過程,它以產品數據集為中心,以數字量傳遞為基礎,利用數字化裝配工藝規劃,數控設備的自動鉆鉚,數字化測量設備的測量定位等技術,使產品在裝配過程中真正得到有效控制,建立起一套有效的產品發放過程控制機制以及相關的工作規范和制度,以保證生產效率和產品質量。
數字化裝配技術體系
飛機數字化裝配技術體系涉及了裝配工藝規劃、數字化柔性定位、裝配制孔連接、自動控制、先進測量與檢測以及系統集成控制等眾多先進技術和裝備,是機械、電子、控制、計算機等多學科交叉融合的高新技術集成。依據飛機裝配的工藝流程,可將數字化裝配技術體系歸納為7個方面:
數字化裝配工藝設計。數字化裝配工藝設計的基礎是基于模型的定義(MBD)技術,即用集成的三維實體模型來完整表達產品定義信息,作為唯一的制造依據。MBD技術根據數字化定義規范,采用三維建模進行數字化產品定義,建立起滿足協調要求的全機三維數字樣機和三維工裝模型。
裝配定位技術。裝配定位技術主要分為工裝定位和零件裝配基準孔面自定位兩個方面。裝配工裝在飛機裝配過程中被大量采用以保證進入裝配的飛機零件、組合件、板件及段件精確定位。柔性工裝克服了剛性工裝剛性專用、設計制造周期長、存儲占地面積大,結構開敞性較差等缺點,具有柔性化、數字化、模塊化的特點。
裝配制孔技術?,F代飛機結構件采用的主要連接方式仍為機械連接,新型飛機對改善各連接點的技術狀態(表面質量、配合性質、結構形式等)提出了很高要求,復合材料的大量采用更帶來了大量復合材料的制孔需求,單純依靠傳統的手工制孔,很容易出現復材分層、孔徑橢圓等故障,產品質量難以保證。解決這些問題的最重要途徑是通過改善制孔工藝方法,采用自動化手段進行連接孔的精確定位和制備,以提高制孔質量和效率。
裝配連接技術。飛機制造中裝配連接質量直接影響飛機結構的抗疲勞性能與可靠性。高性能航空器的機械連接結構必須采用先進的連接技術;另一方面,先進標準連接件的選取和安裝工藝(如安裝工具、干涉量的確定等)也應作為裝配連接技術研究的重要內容。
數字化檢測技術。數字化檢測技術已成為打通飛機復雜零件與大尺寸零部件設計、制造、裝配、檢測一體化流程,提升檢測效率與水平的關鍵環節。應采用基于數字化檢測設備(坐標測量機、激光跟蹤儀、激光雷達、激光掃描儀等)的產品三維檢測與質量控制手段,建立數字化檢測技術體系,開發計算機輔助檢測規劃與測量數據分析系統,制定相應的數字化檢測技術規范,以實現提高檢測效率與質量的目標。
系統集成與控制技術。系統集成與控制技術是實現交互與協調的基礎,它將數字化裝配技術中各支撐單元即所有自動化裝配設備、傳感器、測量設備通過通訊網絡集成在一起,共享信息,形成一個協調運作的全閉環控制系統。
裝配抗疲勞強化技術。飛機主要的裝配抗疲勞強化工藝方法包括滾壓、擠壓、干涉配合及拋光處理等,而長壽命機械連接則包括高鎖螺栓連接、冠狀鉚釘等。
數字化裝配工程應用情況
中航工業成飛緊緊瞄準國外發達國家飛機制造過程中數字化裝配技術的發展,結合我國國情和公司的發展規劃,在“實現自主創新、提升核心技術和能力”目標的指引下,在數字化裝配領域進行了積極并卓有成效的探索,通過全面實現裝配工藝設計、精確定位、制孔、部件對合與精加工以及檢測監控、過程管理的數字化來建立數字化裝配生產線和構建完整的數字化裝配體系,對數字化裝配系統提出了三個“基于”的要求,即:基于裝配流程以保證工藝繼承性,基于測量的數字量協調、傳遞與控制以保證制造環節的閉環性,基于數模驅動以保證制造依據的唯一性和操作的便利性,最終采用“開放式伺服移動裝配定位平臺+數控五坐標多作業單元移動龍門制孔機床”的結構形式,分離裝配定位系統與制孔設備,實現了人工作業與設備自動作業的解耦。
數字化裝配技術代表了當今飛機制造的發展方向,涉及多學科的綜合研究與應用,其研究必須與工藝技術、實驗技術、檢測技術和現代管理等技術的研究相結合,以實現生產模式和方法的轉變。深入研究并逐步應用數字化裝配技術,在提升產品質量和生產效率的同時,更能促進我國航空產品生產的觀念性改變及管理體制的變革,攻克我國飛機裝配及制造技術中的薄弱環節,實現飛機制造技術水平的重大突破。
數字化技術在強度試驗中的應用
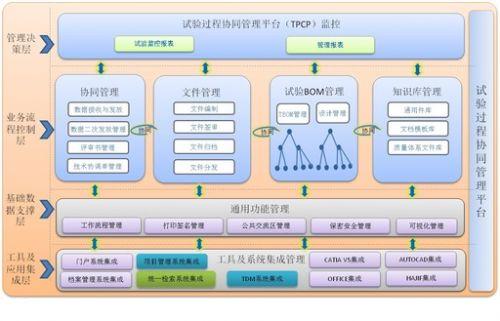
強度所數字化協同試驗平臺
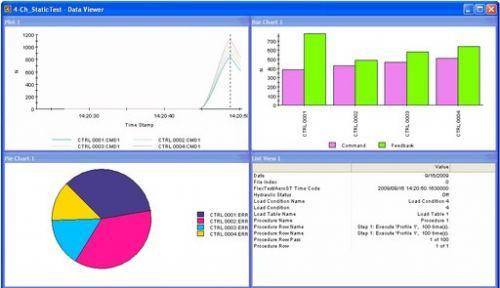
強度所數字化試驗協調加載控制系統
中航工業強度所 蔡芳 劉思揚
中航工業強度所作為國家負責承擔全尺寸飛機結構地面強度驗證試驗的專業研究機構,也在不斷變革傳統的試驗模式,采用數字化手段,將數字化技術深度融入強度試驗的每一個環節,充分提升物理試驗的準確性,降低物理試驗風險,提高驗證試驗效率。
數字化試驗設計
數字化試驗設計是根據試驗件數字模型和試驗加載要求確定試驗工藝及程序。在傳統條件下,基于空間和時間的確定性關系來完成試驗設計工作,試驗設計技術狀態依靠人員監控來確認,難以實時掌握試驗過程中工況變化并及時調整,導致試驗設計質量一致性不穩定,試驗裝配質量波動較大。數字化設計實現了試驗件及支持系統設計、載荷處理系統設計、載荷施加設計、液壓系統設計、試驗控制設計、測量系統設計的數字化及其關聯。數字化設計輸入是包含試驗項目、試驗目的、使用載荷、設計載荷等的試驗任務書和飛機型號的數字樣機。
飛機結構強度領域的數字化試驗協調加載控制主要包括數字化液壓缸、自適應協調加載控制系統、自動化設備管理系統、智能校驗與檢測裝置、智能傳感識別及數據采集裝置、多場精準測量系統等,能夠對試驗過程中力、扭矩、充壓、液壓、應變、位移、圖像等信息進行實時監測、采集與定位,實現基于強度試驗系統工程的試驗風險預警自主決策、自適應協調加載控制、設備故障診斷等。
試驗件數字化裝配基于試驗設計結果、MBD技術等,在計算機環境中,將試驗件和試驗設備模型,通過分析、虛擬模型、可視化和數據表達,進行虛擬環境中的裝配關系工程決定。數字化試驗裝配是驗證、優化強度試驗設計結果的必然趨勢,主要采用各種智能的或基于知識工程的算法,以全自動方式或者部分人工干預手段,提高裝配執行的可操作性和人機功效,有效地提升裝配效率、預防裝配干涉。
數字化協同試驗平臺
數字化協同試驗平臺是依托數字化技術建設的飛機一體化協同研發平臺。該平臺作為強度所貫穿試驗管理與試驗流程執行的系統平臺,對外實現強度所與各協作單位(上級單位、主機設計單位、適航管理部門等)之間的數據交換與協同,對內實現所內的異地試驗協同與綜合管控(西安總部、閻良新區、上海分部、長安基地),同時將質量控制融入試驗過程的多個環節,實現了質量控制與試驗過程的協同以及試驗全過程單一數據源管理。
強度所在國內首次提出了強度試驗BOM(TBOM),第一次從飛機結構強度試驗的角度進行分解,構建強度試驗的樹形結構,用以組織試驗各個環節產生的各類圖文檔數據,滿足各級參試人員對試驗過程信息管理、查看及使用需求。TBOM是對飛機型號研制BOM的完美補充,也是融入飛機一體化協同研發環境的統一語言平臺
近年來,強度所在C919大型客機、AG600大型滅火/水上救援水陸兩棲飛機的全機靜力試驗過程中,數字化協同試驗平臺發揮了重要作用。
虛擬試驗
虛擬試驗是新型飛機數字化設計/制造/試驗流程中的重要一環。虛擬試驗是在虛擬現實環境中,對數字化物理模型進行的試驗。具體地說,飛機結構強度虛擬試驗是以仿真、虛擬現實技術、知識工程為基礎,以試驗流程為導向,在虛擬樣機上對產品進行驗證的過程。虛擬試驗與物理試驗相結合,可用于指導物理試驗,為結構設計提供快速可靠的響應反饋,是一種新的試驗模式。虛擬試驗可以減少或部分替代物理試驗,完成物理試驗難以實施的驗證,降低研制風險,縮短研制周期,減少研制成本。
虛擬試驗驗證技術是飛機結構強度試驗技術發展的必然趨勢。虛擬試驗驗證技術不僅適用于飛機可行性論證、方案論證、研制生產等全壽命周期,而且也適應于民機適航認證過程。通過各個階段的虛擬試驗驗證獲得充分可信的飛機結構強度性能,從而減少飛機結構研制過程中的不確定性。
強度所已結合多個機型,如ARJ21-700及C919等壁板級、部段級乃至全機級試驗開展了虛擬試驗,進行了試驗與分析相關性評估的應用研究,并利用試驗數據對虛擬試驗分析模型與結果進行評估驗證,取得了非常良好的效果。虛擬試驗已在并將在更多型號試驗中發揮重要作用。
試驗數據實時分析與評估
由于全機靜力試驗成本高、周期長,現在進行全機靜力試驗過程中,大量的試驗數據在試驗現場無法及時實時觀測、分析、做出判斷和預測。為了及時在試驗現場全面掌握試驗測試數據,確保試驗安全,強度所在多年試驗的基礎上開發了試驗數據顯示與一致性評估軟件,建立一套全機靜力試驗快速評估系統,可有效提高全機靜立試驗水平,目前已在中航工業等多家單位開展應用,取得了良好的社會效益和經濟效益。其主要功能包括:試驗數據的實時顯示和分析、試驗數據與分析數據的實時比較、試驗數據的查詢、分析、修正和統計、試驗數據與分析數據的一致性分析和評估以及三維實時顯示。
隨著“十三五”規劃進程的不斷推進,強度所也制定了自己的發展目標:以智能化為方向、以數字化為突破口,實現信息化系統覆蓋80%以上的業務,建立覆蓋全業務的流程管理系統,建設基本完備的試驗數據管理體系,初步實現數字強度。
數字化制造體系助推沈飛快速發展
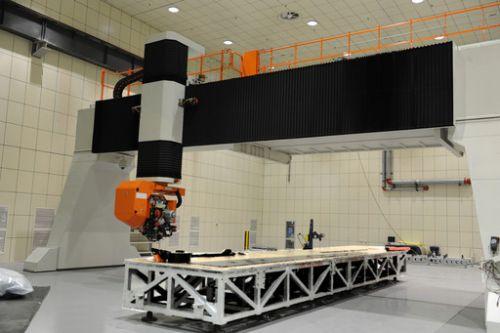
沈飛自動鋪帶機
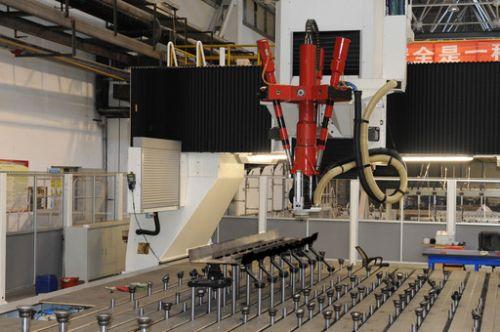
沈飛五坐標柔性加工中心
中航工業沈飛 洪杰 劉琳
中航工業沈飛從20世紀80年代開始進行計算機和數控技術的研究與應用工作。在殲8Ⅱ飛機的研制中,首次規模采用數控加工技術,提高了飛機零部件的制造精度和協調準確度,縮短了飛機研制周期。 “九五”期間,沈飛公司以波音737飛機轉包生產為契機,開始系統進行數字化基礎建設,在數字化協同設計、零件數控加工、工裝數字化設計和制造等方面取得了突破性進展,為數字化技術全面應用奠定了堅實基礎。
進入21世紀,沈飛公司抓住信息技術迅猛發展的機遇,不失時機地用信息技術改造傳統制造技術,迅速提高了飛機制造的能力和水平。2006年起, 沈飛公司充分利用原國防科工委組織實施“飛機制造業數字化工程”的難得機會,開始系統進行飛機數字化生產方式的研究和應用。“飛機制造業數字化工程”主要是通過整合和充分利用現有條件,借鑒國外先進的數字化技術應用及其管理模式,開展技術攻關,基本建立飛機研制的數字化基本體系,形成飛機全機數字樣機研制和典型部件的數字化研制能力。根據統一部署,沈飛公司與沈陽所共同承擔“工程總成”項目(包括工程總體與集成、并行產品數字化定義、產品數據管理系統、數字化設計試驗和制造流程、協同工作平臺、工程驗證),并獨立負責主要的三條數字化生產線項目。經過近10年的研究和實施,沈飛公司承擔的數字化工程科研項目全部完成了預定內容,順利通過了中航工業組織的項目驗收。這標志著沈飛公司已經建立了飛機數字化研制基本體系,打通了飛機數字化生產線。十余年來,飛機數字化研制基本體系支撐著沈飛公司承擔的多項國家航空武器裝備研制生產,促進了飛機制造的大跨越。
正是依靠現代信息技術與制造技術的相互融合,沈飛公司實現了生產方式的根本性變革,形成了一套以數字量為特征的技術協調體系,全面應用數字化的三維設計、虛擬裝配、并行工程,實現了從設計到飛行的全面數字化,取得了飛機研制的新突破,極大地縮短了飛機研制周期,降低了研制成本。例如,在飛機研制中,實現了:數字樣機取代物理樣機;取消模線樣板,專用工裝由30000余項減為13000余項,標準量規由1835項減少為28項;縮短型號研制周期一年;制造質量顯著提高,工裝返工率由300%減少到21%。
2009年,在沈陽召開的數字化工程現場經驗交流會上,沈飛公司提出和實踐的數字化生產模式得到了大會的充分肯定,稱其“為飛機廠所數字化發展確定了方向和重點,為進一步推進主機廠所數字化能力建設提供了寶貴經驗”。
相對于傳統的飛機制造模式,數字化制造將帶來全新的變革:數字化的生產方式下,工程技術人員基于網絡化的協同工作環境,以產品數字樣機為核心,根據設計結果成熟度的變化,不斷追蹤產品的設計狀態,協同進行產品、工藝、工裝的設計工作。在傳統的飛機制造中,基于飛機結構的特點,必須按照模擬量傳遞的原則采用模線樣板工作法,以此作為生產中傳遞飛機外形和結構的幾何形狀和尺寸的原始依據。在飛機數字化制造方式中,數字量傳遞替代了模擬量傳遞的協調方法,數字樣機成為了唯一的數據源,為并行工程創造了良好條件。數字化的制造方式,建立了數字化設計制造流程,改變了人們的工作職責和相互關系。企業必須按照數字化制造的特點,優化業務流程,調整勞動生產組織,按照物流、信息流同步的原則,實現資源優化配置。數字化的制造方式,依賴于大量的基于數字化技術驅動的工藝裝備,這是企業開展數字化制造的硬件基礎和基本手段。打通數字化生產線必須研制各類數字化專用工藝裝備,包括蒙皮多點成型設備、柔性多點夾持裝置、復材自動鋪帶機、自動鉆鉚機、柔性裝配平臺等。飛機數字化制造體系關系到飛機研制的協調方法、各專業的制造技術、生產方式、組織形式、技術基礎等多方面內容,各方面相互依存和關聯,構成有機的整體。其中,數字化標準、基礎數據庫是體系的基礎;各類軟件資源及支持協同設計制造的網絡是支撐環境;并行產品數字化設計、數字化制造、數字化管理、各條生產線通過基礎和支撐環境的支持,構成飛機數字化制造工作主體。
為了實現上述變革,沈飛公司提出:必須努力構建和應用一個平臺(數字化協同平臺),打通六條數字化生產線(數字化切削加工生產線、數字化復合材料構件生產線、數字化鈑金生產線、數字化焊接生產線、數字化裝配生產線、數字化工裝生產線),建設四個中心(制造數據中心、工藝仿真中心、物料配送中心、生產管控中心),形成飛機數字化制造體系,從而全面提升數字化制造水平與能力。通過數字化工程的建設,沈飛公司基本上完成了由傳統的飛機制造方式向數字化生產方式的轉變,企業核心競爭力有了極大提高。智能制造基本思路是將互聯網技術或物聯網技術、工業自動控制技術、企業信息集成與優化技術以及數字化設計制造技術高度集成化。為此,沈飛公司將結合《中國制造2025》戰略,著力開展智能制造技術規劃與研究。面向智能制造領域,將以基于物聯網開展智能制造領域技術研究為切入點,開發相關智能制造應用管控系統,形成基于物聯網的自動化、智能化制造技術支持能力。
數字化工程的成功極大地促進了沈飛公司國家重點工程的研制工作,數字化技術所帶來的優勢效果已越來越令人刮目相看,數字化技術正向人們展示著無窮的魅力。