天然橡膠具有高強(qiáng)度、高彈性、大變形等優(yōu)異的物理力學(xué)性能,是最早也是應(yīng)用范圍最廣泛的通用橡膠之一。由于其制品很多是在周期應(yīng)力作用下使用,因此對(duì)天然橡膠疲勞行為及疲勞機(jī)理的研究具有重要意義。目前國(guó)內(nèi)外對(duì)于天然橡膠疲勞性能的研究主要集中在通過(guò)研究天然橡膠的疲勞破壞斷面,從力學(xué)角度對(duì)天然橡膠的疲勞破壞過(guò)程做出解釋,以及天然橡膠制品的使用壽命預(yù)測(cè)上,對(duì)于在疲勞及疲勞破壞過(guò)程中天然橡膠的分子結(jié)構(gòu)以及交聯(lián)網(wǎng)絡(luò)結(jié)構(gòu)變化的研究相對(duì)較少。
目前國(guó)內(nèi)外提出的橡膠疲勞機(jī)理主要是兩類(lèi):機(jī)械破壞理論與力化學(xué)理論。其中機(jī)械破壞理論認(rèn)為橡膠的疲勞老化不是一個(gè)化學(xué)反應(yīng)過(guò)程,而純粹是由所施加到橡膠上的機(jī)械應(yīng)力使其結(jié)構(gòu)及性能產(chǎn)生變化,以致最后喪失使用價(jià)值的過(guò)程;如果說(shuō)在這個(gè)過(guò)程中有化學(xué)反應(yīng)產(chǎn)生的話,那也只能認(rèn)為是影響疲勞過(guò)程的一個(gè)因素。如藤本等認(rèn)為在周期性應(yīng)力的作用下,含有填料的硫化膠中首先發(fā)生了應(yīng)力松弛現(xiàn)象,然后硫化膠高次結(jié)構(gòu)會(huì)發(fā)生變化,其中填料周?chē)纬傻南鹉z相會(huì)向不均勻化方向轉(zhuǎn)變,并形成較大的聚集結(jié)構(gòu),成為宏觀的應(yīng)力集中點(diǎn),容易導(dǎo)致裂紋的形成,進(jìn)而發(fā)生破壞。
力化學(xué)理論則認(rèn)為,橡膠的疲勞老化過(guò)程是在力的作用下的一個(gè)活化氧化過(guò)程,是化學(xué)鍵斷裂的結(jié)果,即試樣在周期性應(yīng)變過(guò)程中,應(yīng)力不斷集中于“弱”鍵處,由于裂紋尖端處的分子鏈處在高應(yīng)力場(chǎng)中,分子鏈拉長(zhǎng)。當(dāng)應(yīng)力達(dá)到鍵的強(qiáng)度時(shí),發(fā)生鍵斷裂誘發(fā)微細(xì)裂紋,在高度應(yīng)力集中的情況下,裂紋尖端處的分子鏈產(chǎn)生黏彈性伸長(zhǎng)至斷裂。當(dāng)足夠多的分子鏈斷開(kāi)時(shí),裂紋尺寸將增加一個(gè)微小的增量,是隨時(shí)間而發(fā)展并涉及分子鏈連續(xù)斷裂的黏彈性非平衡過(guò)程。但具體反應(yīng)過(guò)程,不同的研究者尚存在一定的分歧。Gent通過(guò)對(duì)NR疲勞老化研究后認(rèn)為,在疲勞過(guò)程中橡膠分子鏈被機(jī)械力打斷,由此所產(chǎn)生的自由基與氧反應(yīng),引發(fā)了氧化老化。因此,由分子鏈切斷而形成的裂紋的頂端附近隨著老化的進(jìn)行使強(qiáng)度降低。Kuzu—minskii則認(rèn)為,與力學(xué)破壞相比,更可能發(fā)生的是應(yīng)力活化的氧化破壞,即橡膠會(huì)與氧發(fā)生反應(yīng)生成過(guò)氧化物,然后橡膠分子鏈產(chǎn)生斷裂,防老劑的加入使得在分子鏈斷裂之前過(guò)氧化物即與防老劑發(fā)生反應(yīng),奪取其中的氧,從而避免了橡膠分子鏈的斷鏈。但在反復(fù)變形的作用下,橡膠分子主鏈的鍵變?nèi)酰瑥亩蛊渑c氧反應(yīng)所需要的活化能降低,促進(jìn)了氧化反應(yīng),導(dǎo)致硫化膠的物理性能發(fā)生變化。
但這些研究主要是基于拉伸或壓縮應(yīng)力下,通過(guò)對(duì)疲勞過(guò)程中橡膠性能或一些物理參數(shù)的變化進(jìn)行分析,而對(duì)于橡膠在疲勞過(guò)程中出現(xiàn)的一些現(xiàn)象及疲勞產(chǎn)物研究較少。
本工作主要從一維受壓狀態(tài)下剪切疲勞過(guò)程中天然橡膠的疲勞產(chǎn)物的分析人手,通過(guò)剪切疲勞前后天然橡膠硫化膠組分的對(duì)比,研究硫化膠在疲勞過(guò)程中的化學(xué)變化,同時(shí)從微觀層面對(duì)天然橡膠疲勞過(guò)程進(jìn)行研究。
1 實(shí)驗(yàn)
1.1 天然橡膠膠料的制備
首先將天然生膠在雙輥煉膠機(jī)上塑煉5min,然后依次加入SA、ZnO、防老劑、炭黑、NOBS、S,薄通后出片,在室溫下至少停放8h后返煉。基本配方為(phr):1號(hào)煙片膠NR(印尼1#煙片膠,上海多康實(shí)業(yè)有限公司)100;SA(工業(yè)純,淄博市淄川匯通油脂精細(xì)化工廠)1;ZnO(工業(yè)純,山東匯苑化工廠)5;防老劑OD(工業(yè)純,華星(宿遷)化學(xué)有限公司)0.5;防老劑ODA(工業(yè)純,華星(宿遷)化學(xué)有限公司)0.5;促進(jìn)劑NOBS(工業(yè)純,黃巖浙東橡膠助劑有限公司)1.1;硫磺S(工業(yè)純,衡水天順橡膠化工有限公司)2;炭黑N774(工業(yè)純,東莞市齊德利化工科技有限公司)18。
1.2 剪切疲勞試樣的制備
剪切疲勞試樣為四板剪切試樣(參考GB/T12830--2008)(如圖1)。將返煉后的膠料,通過(guò)注壓硫化黏結(jié)成所需規(guī)格的試樣,硫化時(shí)間45min,硫化溫度143℃±3℃,壓力10MPa,采用的膠黏劑為Chemlok205和Chemlok220(Lord公司制造)。

圖1 四板剪切試樣示意圖
1.3 剪切疲勞試驗(yàn)本試驗(yàn)
用MPC-2格拉西里疲勞試驗(yàn)機(jī)進(jìn)行試驗(yàn),先對(duì)試驗(yàn)機(jī)進(jìn)行初始設(shè)置,即試樣應(yīng)變值設(shè)定為100%,加載頻率設(shè)為5Hz。然后將上下夾具調(diào)至間距最小狀態(tài),此時(shí)將四板剪切試樣兩端的金屬接頭用夾具夾緊,保證在試驗(yàn)過(guò)程中金屬接頭與卡具間不發(fā)生相對(duì)位移,試樣即安裝完成,可開(kāi)始進(jìn)行疲勞試驗(yàn)。在實(shí)驗(yàn)過(guò)程中,定期(4~12h,隨疲勞進(jìn)程逐漸縮短觀察間隔)對(duì)試樣疲勞現(xiàn)象進(jìn)行觀察并記錄現(xiàn)象。
1.4 凝膠色譜分析(GPC)
采用M302TDA凝膠滲透色譜分析儀進(jìn)行測(cè)試。選取四氫呋喃為溶劑,以5mg/mL濃度對(duì)試樣進(jìn)行溶液配制。
1.5 衰減全反射紅外光譜測(cè)試(FTIR-ATR)
采用Magna750紅外光譜儀進(jìn)行測(cè)試。將待測(cè)試樣鋪在透鏡中央,再將測(cè)試的探針輕輕壓在試樣上表面,旋緊扣鎖后開(kāi)始測(cè)試。測(cè)試完畢后應(yīng)用OMMEC軟件對(duì)測(cè)試結(jié)果進(jìn)行處理及分析。
1.6 氣相色譜-質(zhì)譜聯(lián)用技術(shù)測(cè)試(GC-MS)
采用ZAB-HS色譜一質(zhì)譜聯(lián)用分析儀進(jìn)行測(cè)試。選取甲苯作為萃取劑對(duì)油狀物進(jìn)行萃取。
2 結(jié)果與討論
2.1 實(shí)驗(yàn)現(xiàn)象及產(chǎn)物
實(shí)驗(yàn)中發(fā)現(xiàn),當(dāng)試樣經(jīng)過(guò)剪切疲勞60~72h后,剪切疲勞試樣的橡膠裸露部分出現(xiàn)裂紋,裂紋長(zhǎng)度約1~2mm,并隨著疲勞進(jìn)程裂紋逐漸擴(kuò)展,當(dāng)疲勞時(shí)間達(dá)到160~180h后,裂紋長(zhǎng)度擴(kuò)展至20~30mm,同時(shí)有極為黏稠的黑色油狀物質(zhì)溢出于裂H邊緣,并且伴隨整個(gè)裂紋擴(kuò)展過(guò)程不斷增加。疲勞裂紋及產(chǎn)物如圖2所示。
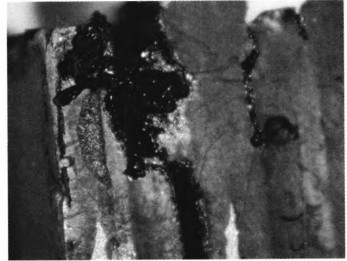
圖2 天然橡膠硫化膠試樣剪切疲勞油狀產(chǎn)物
2.2 疲勞產(chǎn)物的化學(xué)分析
按照“溶度參數(shù)相近相溶”原則,由于天然橡膠的溶度參數(shù)為17.4(J/cm3)1/2,選取溶度參數(shù)為17.6(J/cm3)1/2的二甲苯作為溶劑;將天然橡膠生膠、疲勞過(guò)程油狀產(chǎn)物及天然橡膠硫化膠于室溫下同時(shí)浸沒(méi)于二甲苯中,48h后觀察發(fā)現(xiàn),油狀物已完全溶解,溶液呈淡黃色,無(wú)明顯固體物質(zhì);生膠未完全溶解,但達(dá)到極大溶脹,呈淡黃色透明膜狀(如圖3(a)所示);硫化膠僅發(fā)生溶脹,溶液呈透明(如圖3(b)所示),這表明,油狀物為非交聯(lián)的可溶解的小分子物質(zhì)。

圖3 天然橡膠溶解實(shí)驗(yàn)照片
(a)天然橡膠生膠;(b)天然橡膠硫化膠
對(duì)天然橡膠生膠和疲勞油狀物進(jìn)行凝膠色譜分析,結(jié)果(如表l所示)表明,油狀物的各項(xiàng)平均分子量遠(yuǎn)小于天然橡膠生膠,其數(shù)均分子量、重均分子量及Z均分子量為天然橡膠生膠相應(yīng)分子量的1/20左右。一般情況下,在Mz相同時(shí),低分子量成分多時(shí)反映為Mn減少,高分子量成分多時(shí)Mz增大;因此疲勞后,疲勞產(chǎn)物分子量分布明顯變寬,結(jié)合溶解試驗(yàn)表明,疲勞過(guò)程中,硫化膠分子發(fā)生了明顯的分子鏈斷裂現(xiàn)象。
表1 天然橡膠生膠及疲勞試驗(yàn)油狀產(chǎn)物GPC測(cè)試結(jié)果

油狀物的紅外光譜測(cè)試結(jié)果如圖4所示,與疲勞前樣品相比,2917cm-1處的甲基與不飽和雙鍵相連時(shí)的反對(duì)稱伸縮特征峰出現(xiàn)了明顯的減少,同時(shí)在3500cm-1處出現(xiàn)了突出卻不尖銳的醇羥基中O—H鍵的特征峰,在1736cm-1處新的由飽和脂肪酸酯中的C—O的伸縮振動(dòng)特征峰,表明油狀物中含有醇類(lèi)物質(zhì)和酯類(lèi)物質(zhì),這些氧化產(chǎn)物表明疲勞過(guò)程中可能發(fā)生了氧化反應(yīng)。

圖4 油狀物與未疲勞天然橡膠紅外光譜圖
為進(jìn)一步確認(rèn)天然橡膠疲勞油狀產(chǎn)物的化學(xué)組成,對(duì)油狀物進(jìn)行了氣相色譜一質(zhì)譜(GC—MS)分析,檢測(cè)結(jié)果如表2所示。分析表明,天然橡膠硫化膠剪切疲勞降解產(chǎn)物中主要含有(離子流峰高百分比達(dá)1%以上的)長(zhǎng)鏈烷烴(包括正十八烷、正二十烷、正二十一烷、正二十二烷、正二十二烷、正二十三烷、正二十四烷)、硬脂酸、2,8一吩嗪二胺、3,3,-辛基一二苯胺等,酮類(lèi)物質(zhì)、醚類(lèi)物質(zhì)以及酯類(lèi)物質(zhì)應(yīng)是天然橡膠疲勞過(guò)程中由于分子力活化作用氧化得到的產(chǎn)物,這點(diǎn)與紅外光譜中檢測(cè)得到的結(jié)果相符;而較多長(zhǎng)鏈烷烴類(lèi)物質(zhì)的存在則應(yīng)來(lái)自于橡膠分子主鏈上雙鍵的斷裂;疲勞產(chǎn)物中各成分結(jié)果說(shuō)明,硫化膠在剪切疲勞的過(guò)程中橡膠分子主鏈可能發(fā)生了物理斷裂,進(jìn)而發(fā)生氧老化作用;在動(dòng)態(tài)外力的作用下,由分子鏈斷裂產(chǎn)生的部分低分子產(chǎn)物向制品表面發(fā)生遷移,形成了氧化產(chǎn)物與物理斷裂產(chǎn)物的混合體。
表2 油狀物GC-MS測(cè)試結(jié)果
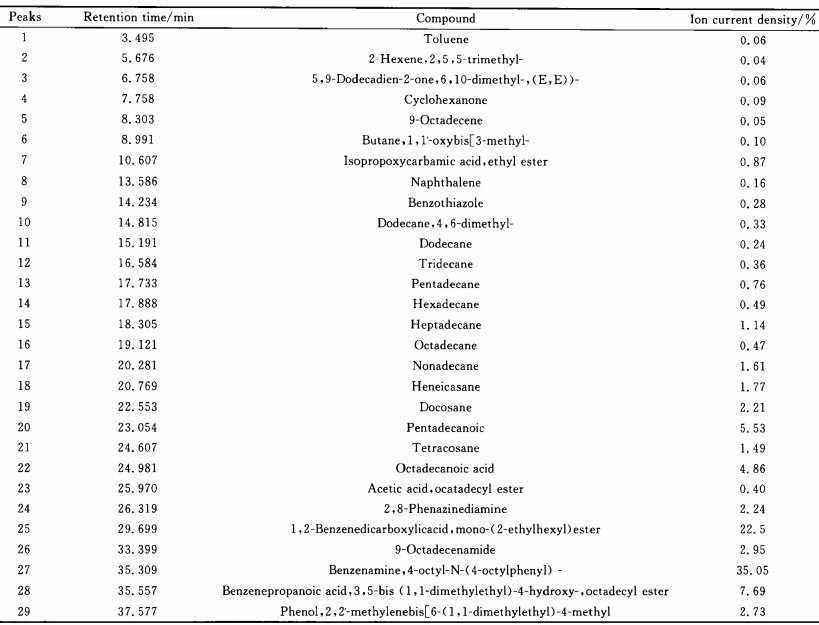
3 結(jié)論
(1)在剪切應(yīng)力作用下,天然橡膠硫化膠疲勞過(guò)程中產(chǎn)生的黑色黏稠油狀物是一種可溶性小分子混合物,主要含有烯烴類(lèi)物質(zhì)、醚類(lèi)物質(zhì)及部分游離態(tài)的添加劑等,說(shuō)明在剪切疲勞過(guò)程中天然橡膠分子主鏈會(huì)發(fā)生斷裂,進(jìn)而發(fā)生氧老化作用,同時(shí)低分子量的部分降解產(chǎn)物和游離態(tài)填料會(huì)向應(yīng)力集中的部位發(fā)生遷移聚集。
(2)天然橡膠硫化膠在疲勞過(guò)程中受到剪切應(yīng)力的作用,部分橡膠分子主鏈及交聯(lián)鍵斷裂后造成硫化膠分子量及交聯(lián)密度的降低,同時(shí)分子鏈上碳原子受活化,化學(xué)鍵變?nèi)酰c氧反應(yīng)的活化能降低,發(fā)生了氧化老化,這也進(jìn)一步佐證了力化學(xué)理論。