引言
密閉加固機箱由于具有良好的抗震動沖擊性能、三防性能和電磁兼容性能而通常應用在機載、星載和野外等嚴酷的環境條件下。隨著芯片集成度及模塊組裝密度的逐步提高,密閉機箱內的熱密度也越來越大,因而對密閉機箱的熱設計要求也越來越高。為保證電子設備在相應的工作環境下長期、穩定地工作,熱設計是必不可少的重要環節。傳統電子設備的熱設計方法是先根據設計者的經驗確定設計方案,然后利用經驗公式進行估算,再通過試驗進行驗證,并根據試驗結果進行優化,最后重新設計生產。該設計方法計算結果準確性較差,設計周期較長,研發成本較高舊。電子設備熱設計軟件可以幫助設計者驗證、優化熱設計方案,滿足產品快速開發的需要,并可以顯著減少產品驗證熱測試的工作量。
1 整機設計
根據某設備研制要求,結合設備重量及安裝空間限制等因素設計了一款密閉加固機箱。為滿足惡劣的環境條件,機箱采用了全密閉的結構形式,采用整體釬焊技術進行制造。在機箱的結構設計中,對機箱中的各模塊和模塊內的元器件進行合理布局,并重視熱傳導在密閉機箱散熱中的作用。
1.1 機箱結構方案設計
首先根據安裝空間以及插件的尺寸和數量,確定機箱基本的外形尺寸為315mm×289.3mm×240mm。機箱內部共有6個模塊:2個電源模塊、1個插板式計算機模塊、1個信號處理模塊和2個微波模塊,它們采用前后排列的方式通過楔形鎖緊裝置豎直安裝在機箱內。所有與外部接口的航空插件等器件都布置在機箱前面板上。母板在機箱的底部,并在母板下方預留出走線空間。該機箱采用鋁合金材質,采用整體釬焊焊接成型。機箱內部各模塊內芯片等發熱元器件的熱量先通過導熱膠墊傳導到導熱板上,通過導熱板傳導到機箱側板上再散發到機箱外部。整個機箱總發熱量約為120W,且主要集中在機箱內部的幾個插件上,僅靠機箱自身的自然散熱無法滿足散熱要求。文中機箱左右側板采用夾層結構,將翅片焊接在側板中間形成風道,通過機箱后部的風機將機箱內部傳導到翅片上的熱量帶走。在導熱板與機箱側板鎖緊位置的接觸部分加工出較高的表面粗糙度,以減小二者之間的接觸熱阻。導熱板為鋁合金材質,應保證一定的厚度,以利于減小熱阻,并對印制板起到支撐作用。機箱的結構形式見圖l。

圖1 機箱結構示意圖
1.2 機箱側板風道設計及風機的選用
考慮翅片的散熱面積及機箱結構外形的限制,初步選取散熱翅片的類型和尺寸。
機箱側板采用夾層結構,將翅片焊接在側板中間形成風道。散熱翅片結構尺寸如圖2和圖3所示。
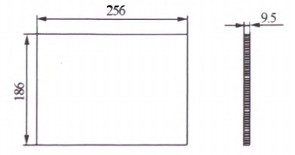
圖2 翅片示意圖

圖3 翅片截面圖
根據設備環境條件最高工作溫度要求,取機箱環境溫度為55℃,按出風口和進風口10℃的溫差,即出風口溫度為65℃,則定性溫度為60℃。60℃時空氣特性參數:空氣比熱Cp=1005J/kg·℃,空氣密度ρ=1.06kg/m3,空氣動力粘度ν=18.97x10-6m2/s。
根據熱平衡方程,按機箱發熱量120W,出風口和進風口10℃的溫差計算,機箱左右風道所需的總風量為:

式中:Q為機箱發熱量;△t為溫差。
每側翅片的通道數n=186/2=93。
空氣的流速為:

式中,S為每個通道的截面積。
翅片型材的每個風道的當量直徑為:

式中:L為風道長度;ξ為局部阻力系數;g為重力加速度。代人數據得:

考慮到計算有一定的誤差,因此選用的風機要有一定的余量,查ehntmpst風機選用手冊,選軸流風機4114NHH,其功率為12.5W,電壓為24V,風量為260m3/h。
2 熱仿真分析
利用FLOTHERM軟件對所建立的機箱結構模型進行熱仿真驗證。在驗證過程中,可對所設定的參數進行調整以獲得更優化的參數。
2 熱仿真分析
利用FLOTHERM軟件對所建立的機箱結構模型進行熱仿真驗證。在驗證過程中,可對所設定的參數進行調整以獲得更優化的參數。
2.1 機箱熱分析模型的建立
(1)外部環境參數的設定
根據設備環境條件最高工作溫度要求,設定機箱的環境溫度為55℃,換熱系數為5W/m2·K。由于機箱是以傳導與對流相結合為主的散熱方式,因此不考慮輻射散熱方式。
(2)建立機箱的簡化幾何模型
真實的機箱中有大量的對熱仿真結果影響不大的信息,而這些信息的存在會大大增加熱模型的復雜度,延長運算時間,因而有必要根據熱設計的實際情況對機箱模型進行簡化。
由于機箱是密封的,傳導在機箱的散熱中起主要作用,因此可忽略機箱內部的對流和輻射換熱方式,對內部各模塊建模時只建立PCB板、芯片、導熱板的模型,而忽略對模塊的屏蔽殼體建模。利用軟件提供的參數化建模方法及模型庫建立芯片級的機箱熱分析模型,如圖4所示。

圖4 機箱熱分析模型
(3)模型的功耗參數
整個機箱總發熱量約為120W,其中,2個電源模塊的發熱量均為40w,1個計算機模塊的發熱量約為20W,1個信號處理模塊的發熱量約為20w,其它2個微波模塊的發熱量可以忽略不計。
(4)設定模型的材質及表面特性
機箱、導熱板的材質為鋁合金。PCB板的導體部分材質為純銅,絕緣部分材質為FR4,導體所占體積比為10%。散熱翅片的建模采用軟件中自帶的散熱器模型,選用詳細結構建模方式。由于機箱采用釬焊焊接,因此在散熱翅片和側板焊接的地方具有可靠的熱傳導途徑,不考慮接觸熱阻,可將側板視為散熱器的基板。
(5)風機模型參數的設定
利用軟件自帶的風機模型功能,按所選用風機的特性參數設定風機模型參數。
2.2 網格劃分
由于機箱兩側的散熱翅片較密,翅片間距為2mm,翅片厚度為0.2mm,因此為提高求解精度,對翅片處的網格進行局域加密處理。另對翅片進行膨脹設置,以消除翅片局域化后延伸線所形成的大量不必要的網格。此外,對翅片在空氣進出I=I處進行膨脹設置后還可以增加該處網格數,詳細求解該處的參數變化,可減少殘差積累。圖5為機箱的網格劃分。

圖5 機箱的網格劃分
2.3 仿真結果及分析
經運算,機箱內部的溫度分布云圖如圖6所示。從圖6中可以看出,機箱內的溫度最高點為板載芯片中心處,且最高溫度為86.6℃,低于90℃這一使用限制要求。

圖6 機箱的溫度分布云圖
3 結束語
本文利用FLOTHERM軟件對所設計的密閉機箱進行了熱仿真驗證,結果顯示該機箱滿足設計要求。同時在實際使用過程中,該機箱能夠較好地適應實際高溫環境,滿足使用要求。通過理論計算與軟件仿真相結合的設計方式可減少相關樣機的研制,可提升產品品質并縮短產品的研發周期。